Deep-See: Towed Opto-Acoustic Vehicle
In early 2017, Dr. Andone Lavery and Dr. Michael Jech (NOAA), along with several additional scientists from WHOI, received funding from NSF to build an optical-acoustic towed vehicle to explore the mid-water, or mesopelagic region, ranging from 200-2000 meters deep. In June, when I became involved with the project, it was in its infancy, merely a proposed layout and some size and weight estimates based on the obsolete WHOI towed vehicle, “BIOMAPER II".
I took the proposal concept and put together a complete vehicle frame and internal sub-system support infrastructure, as well as the mechanisms for deploying, towing, and recovering the instrument safely and effectively from a ship. Early on in the project, we determined that modularity would be beneficial to our scientific goals. The vehicle consists of three separate frames that easily and quickly bolt together in their four corners. The three “modules” are as follows: the forward optical module, which is home to the holographic camera system and two LED lighting arrays; the middle acoustics module, which houses all of the acoustic transducers, their housings, the vehicle’s main power and telemetry housing, the fiber optic termination junction box, and several environmental sensor packages; and the tail module, which is currently mostly vacant room for expansion and mounting structure for the tail panels, which provide hydrodynamic lift and drag for stability.
While I remained in charge of the main design of the vehicle, this project gave me the opportunity to work with more junior mechanical engineers, delegating specific tasks to them and overseeing their designs and integrations with the main system. I supervised Molly Curran in her design of the acoustics transducer and housing mounting configurations, Miles Ochs in his design of the power and telemetry chassis and holographic camera mounting configurations, and Jared Schwartz in his design of a functional deck cart and cradle for enabling easy maneuverability of the vehicle when on the deck of the ship. The final CAD models and fabrication drawings of the main frame weldments, power and telemetry housing, and cable termination junction box I did myself, and I then lead the assembly of the vehicle during the spring of 2018.
After satisfactory testing of the vehicle at the WHOI dock, we took Deep-See aboard the R/V Henry B. Bigelow for a ten-day test and evaluation cruise. During the cruise, I served as the sole mechanical technician, the fiber optics technician, and the manager of all vehicle deck operations. Prior to the cruise, I installed the mechanical termination on the 0.681” electro-optical-mechanical (EOM) cable and ran the cabling inside the ship that would deliver power and telemetry to the winch. Major damage to the ship’s winch’s slip ring was incurred during the ship’s previous cruise, but I was able to repair the fiber and no time was lost to our scientific objectives. Out of seven launches of Deep-See, six were successful in collecting acoustic and optical data in the mesopelagic region. Just one dive was unsuccessful due to the breaking of an optical fiber and loss of telemetry as the vehicle entered the water, but I was able to repair the damage and ready the vehicle for re-launch in just a few hours.
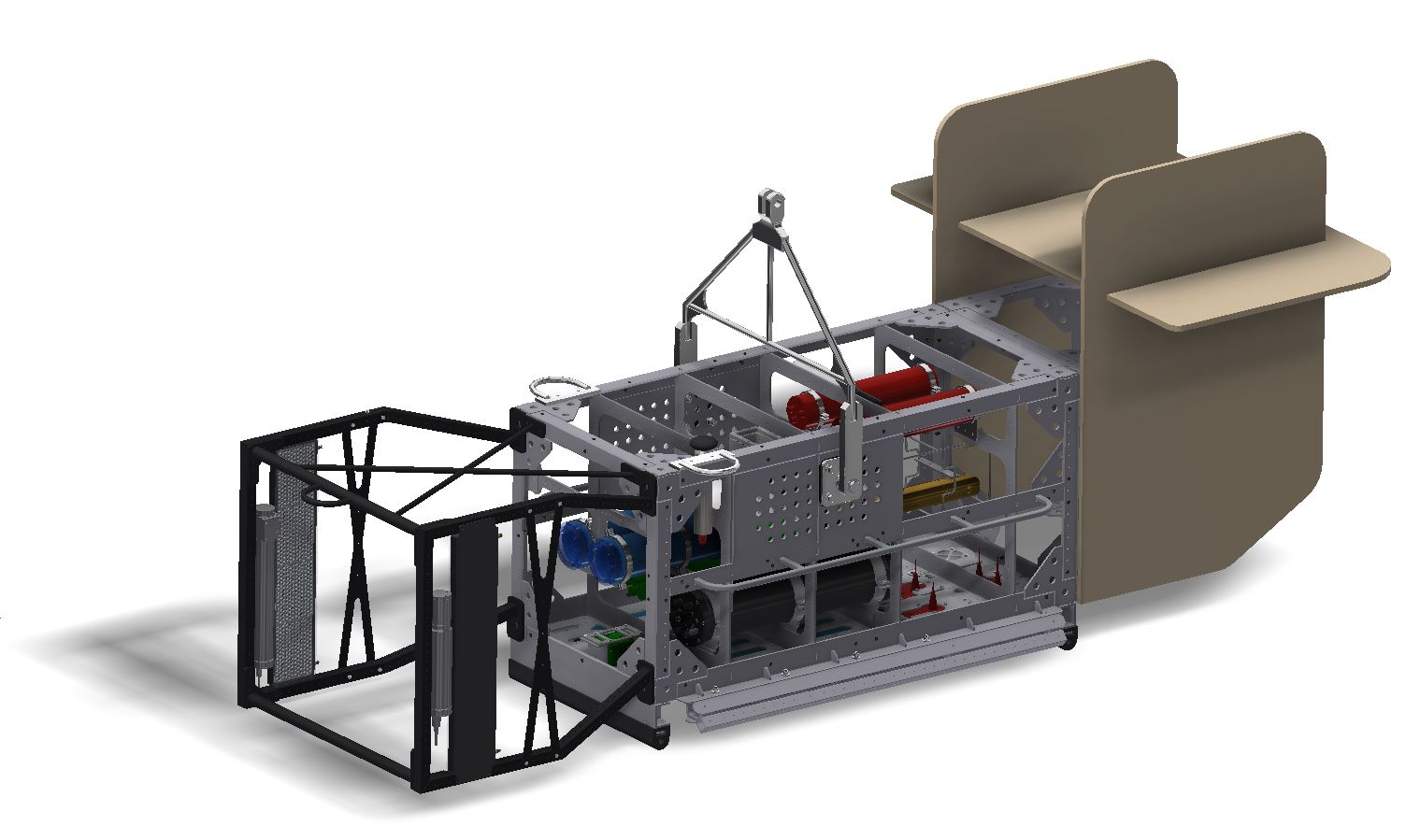
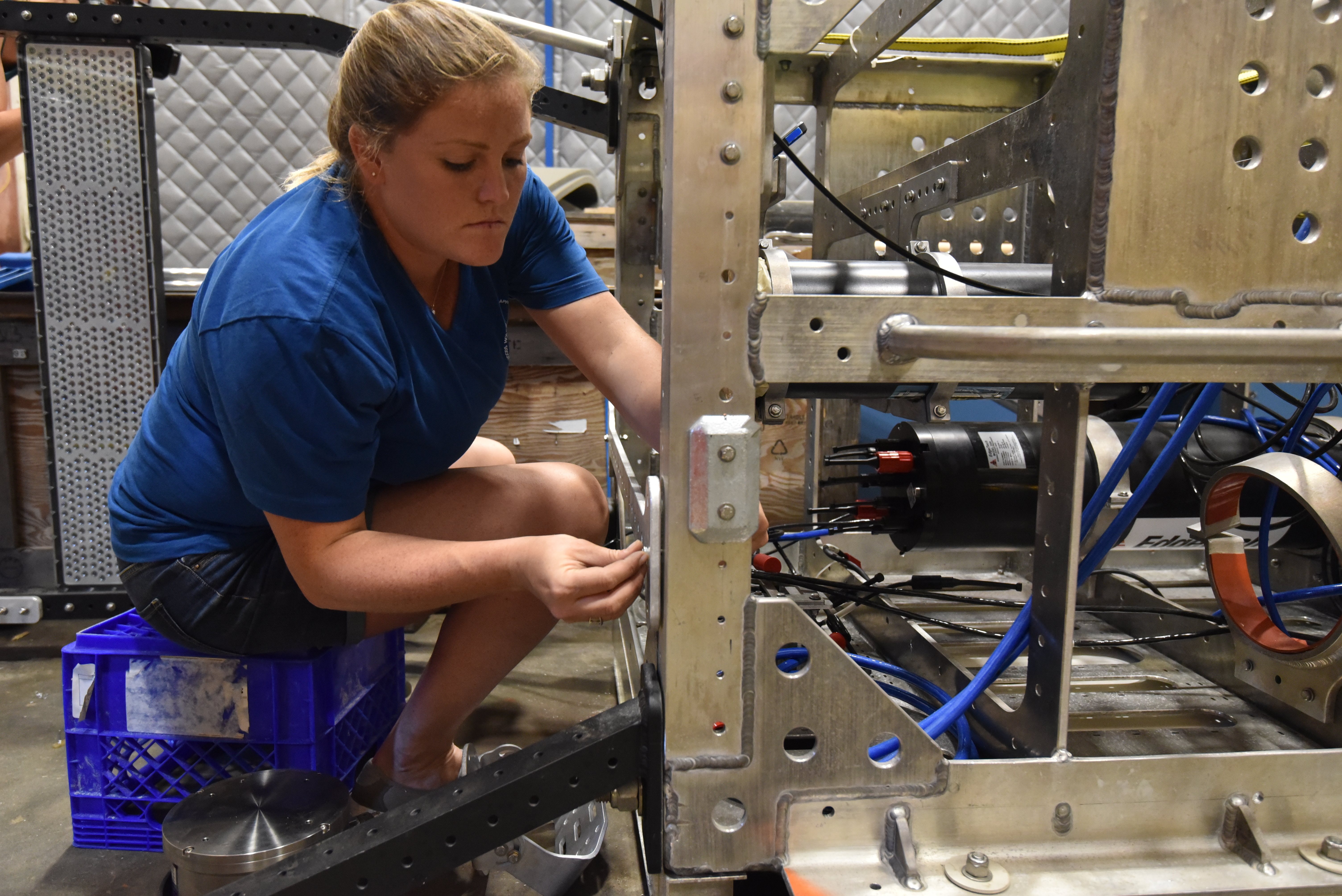
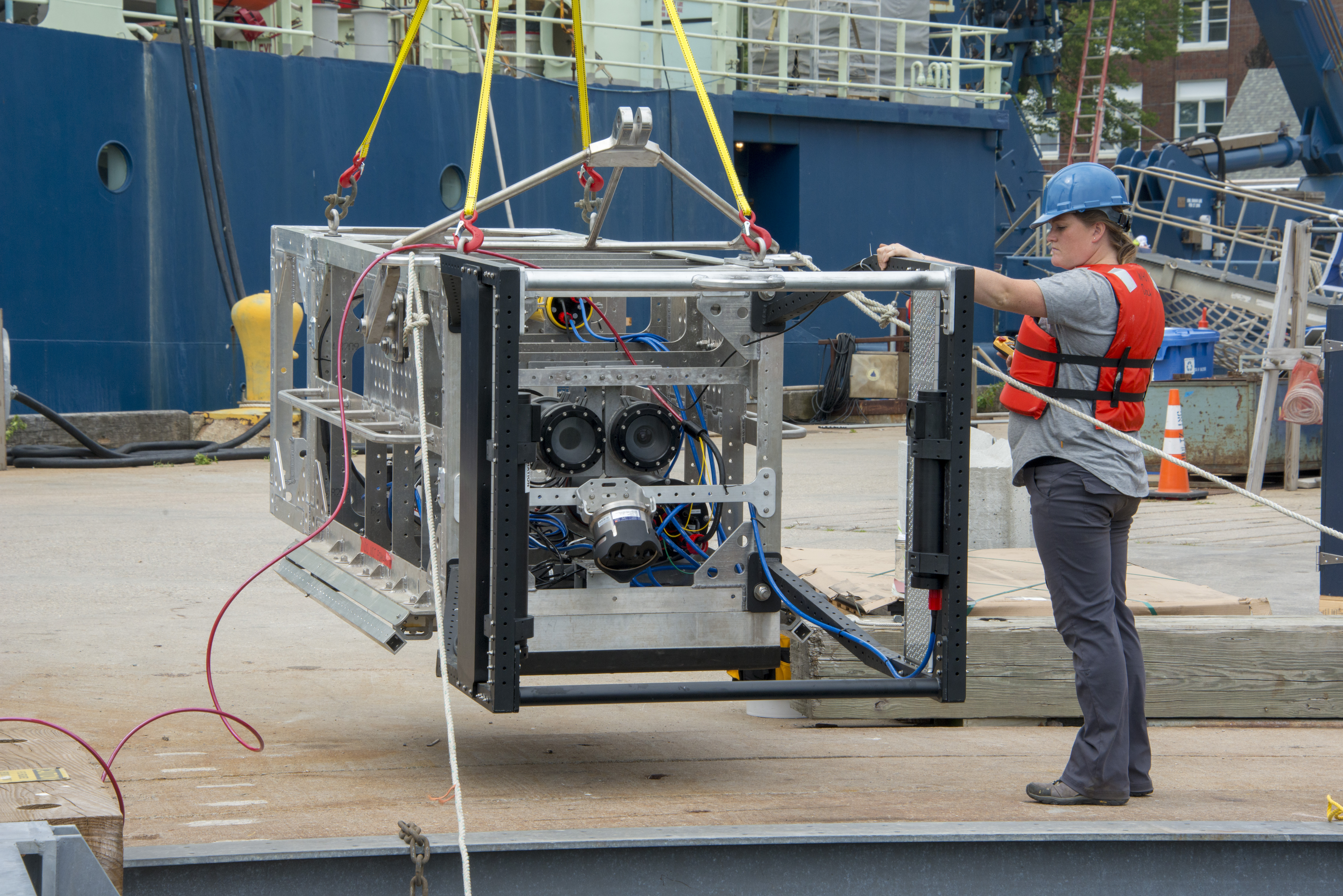
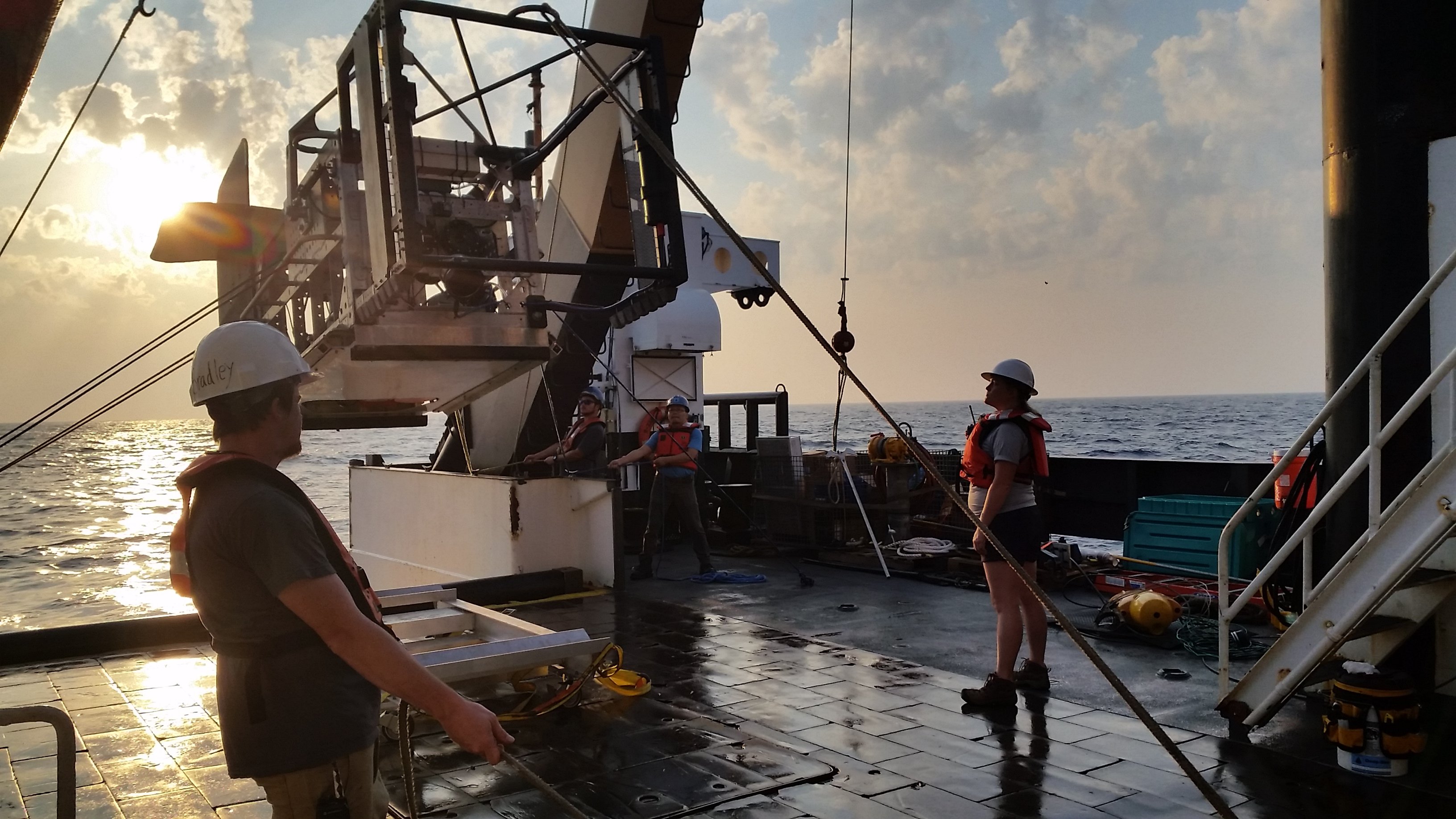