How do Argo floats work?
The typical mission of an Argo float is a 10-day cycle of drifting and taking a vertical series of measurements (profiling). At the surface, the float transmits its GPS position before sinking to a drift depth of 1000 meters. After drifting for approximately 9 days, taking periodic measurements, the float sinks to its full depth of 2000 meters, then slowly rises, measuring conductivity, temperature, and pressure along the way. Salinity can be directly calculated from these quantities. Once it reaches the surface, the float communicates with an Iridium satellite to upload the data and receive any new mission instructions (this takes about 15 minutes to an hour). The cycle repeats until the end of the float’s lifetime, usually around 4 years.
Argo floats are not typically recovered after deployment, but occasionally one will wash ashore or be discovered by a ship.
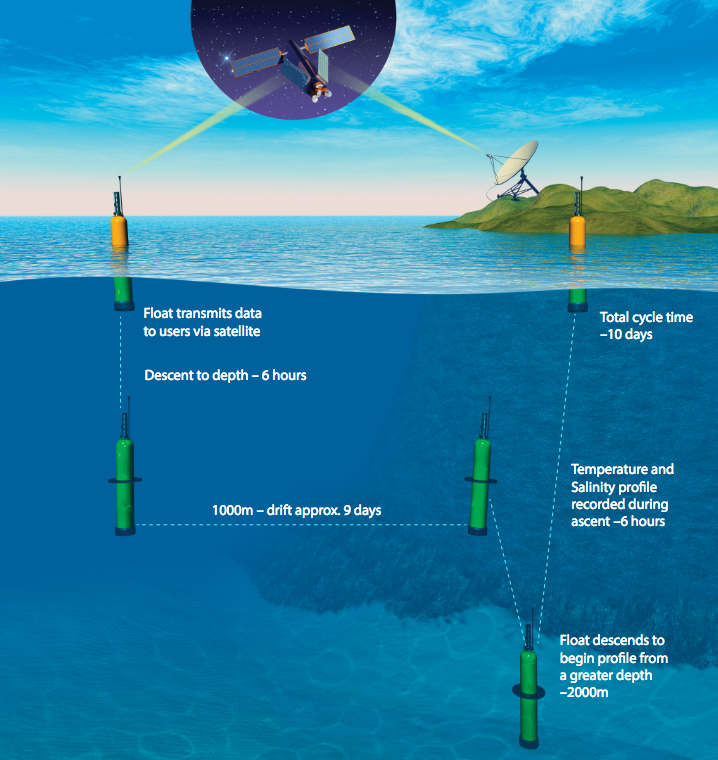
Anatomy of a float
The various models of Argo floats that WHOI deploys have differences in both hardware and software, but share some fundamental components.
Antenna – All Argo floats are topped with an antenna that allows them to communicate with GPS, to transmit their position, and Iridium satellites, to transfer the data collected in the last cycle. The WHOI Argo team can also send new instructions or diagnose problems via these channels. The recent move to the Iridum network allows floats to spend less time transmitting data at the surface, thereby reducing the risk of becoming beached if near to shore. This advance has given the Argo program access to marginal seas such as the Gulf of Mexico.
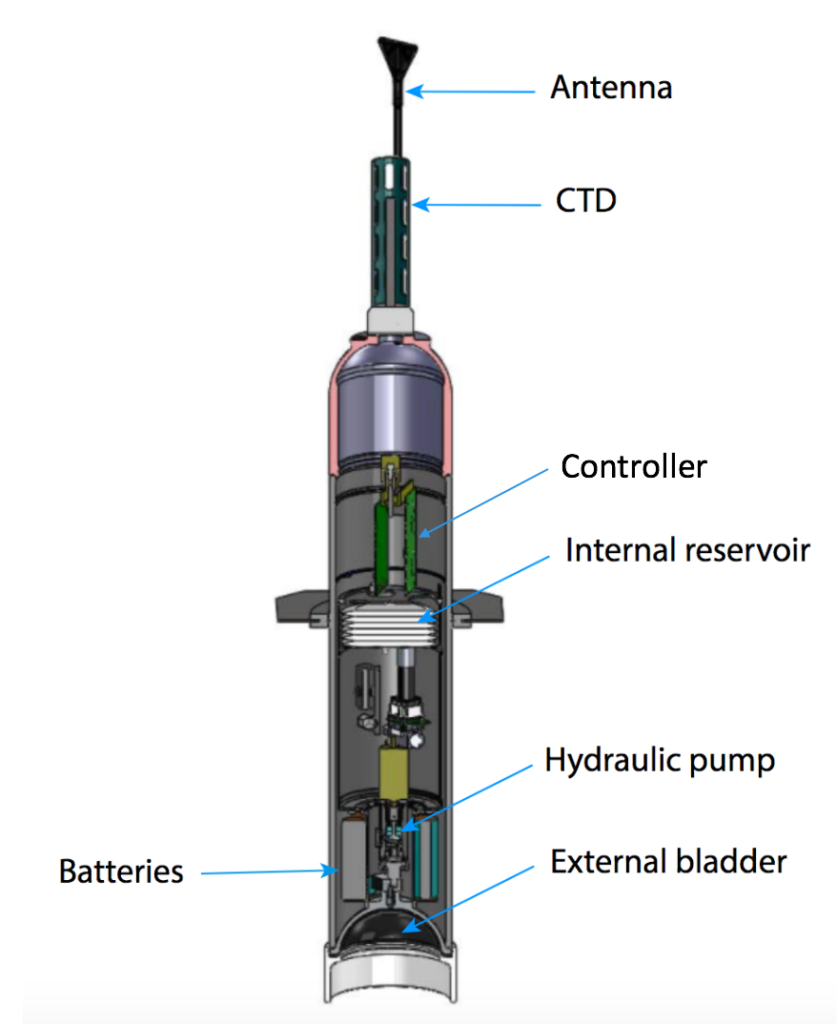
(Courtesy of Michael McClune at Scripps Institution of Oceanography)
Conductivity, Temperature, Depth sensor (CTD) – Also on the top of every Argo float is a set of sensors known as a CTD. They measure temperature within an accuracy of 0.001 degrees C and pressure (closely related to depth) within 0.1 dbar, and calculate salinity using conductivity, temperature, and pressure within 0.001 psu (practical salinity units). Read more about CTDs and their uses in oceanography.
Controller – Each Argo float is controlled by a small computer that contains a program to run the float.
Internal Reservoir – This area of the float stores oil when it is not inflating the external bladder.
Hydraulic pump – This mechanism moves oil between the internal reservoir and the external bladder to control the buoyancy of the float.
Batteries – Modern Argo floats use lithium batteries to power the pumps, sensors, controller, and communication system. The large but finite amount of battery power available is the main limitation on a float’s operational lifetime.
External bladder – Roughly the size of a large grapefruit, this bladder is the mechanism by which Argo floats control their buoyancy. Inflating the bladder with oil from the internal reservoir increases the volume of the float without changing the mass, thereby lowering density and causing the float to rise. Pumping oil out of the bladder back into the reservoir will increase the float’s density, allowing it to sink to a specified depth.
Read more about Argo floats on the International Steering Team website.